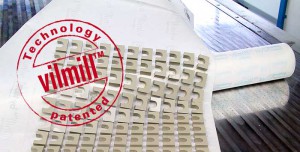
THE DIRECT LINE FOR VILMILL™ CUSTOMERS
Telephone: +49 (0) 35795 337 – 0
Fax: +49 (0) 35795 337 – 33
E-mail: vilmill@portatec.de
ATTENTION! NO VILMILL-Shipping from 09. – 13. June 2025
Telephone: +49 (0) 35795 337 – 0
Fax: +49 (0) 35795 337 – 33
E-mail: vilmill@portatec.de
ATTENTION! NO VILMILL-Shipping from 09. – 13. June 2025
Our location in Neukirch / Schmorkau
Our current video shows the loading, milling and automatic unloading during the production of small parts.
PORTATEC Portal milling machines
PORTATEC is the specialist in the field of the development and manufacture of portal milling machines for large-area cutting of light materials such as aluminium, plastic and fibre-reinforced composite.
The development of PORTATEC portal milling machines established in 1994 in Schmorkau, located about 30 km from Dresden. From the very beginning, Dr D. Metzner and Dr A. Spensberger dedicated themselves to the manufacture of customer-specific milling machines at the highest standards of quality and productivity.
A qualified employee base provides a high potential for creative development and enables quick reaction to futureoriented trends.
Joint research projects with scientific institutes, such as the Dresden University of Technology, as well as innovative concepts, ensure a continuous optimization of our machines.
All machines feature a vacuum clamping table with a large number of program-controlled vacuum fields and powerful claw pumps, which guarantee safe and unmanned operation despite the leakages which arise as a result of the milling process. This is additionally facilitated by the monitoring of all machine functions and by automatic reaction or notification in the event of system failure.
two milling spindles working in parallel at 60,000 rpm for highest productivity with small cutouts
The aircraft industry mills delicate parts using PORTATEC systems in very high batch quantities, at the lowest unit cost and with high process reliability.
The automotive industry requires a high degree of flexibility due to diverse and continuously modified designs.
In plastics machining, a high quality exhibiting superior efficiency and surface quality is achieved using PORTATEC machines.
In aluminium machining, high productivity and precision is achieved using the efficient vacuum clamping tables.
The patented milling underlay vilmill™ guarantees reliable fixing of delicate aluminium or plastic cutouts on the basis of its revolutionary adhesive coating as well as providing additional further advantages in milling processes.
PORTATEC not only supplies the machine. PORTATEC rather supplies technologies which are tailored 100 per cent to the customer’s existing production process. It also provides its customers with highly competent advice in technological questions.
Elaborate solutions for convenient and rapid setting-up, as well as strategies for the energy management of the machine and peripherals, e.g., output control or automatic shutdown, increase the cost-effectiveness of the machine. Further process parameters, such as the strength of the minimum quantity cooling lubrication, can be automatically regulated for every machining step. Exact and accurately repeatable.
SIEMENS control system sets standards in convenient and efficient operation